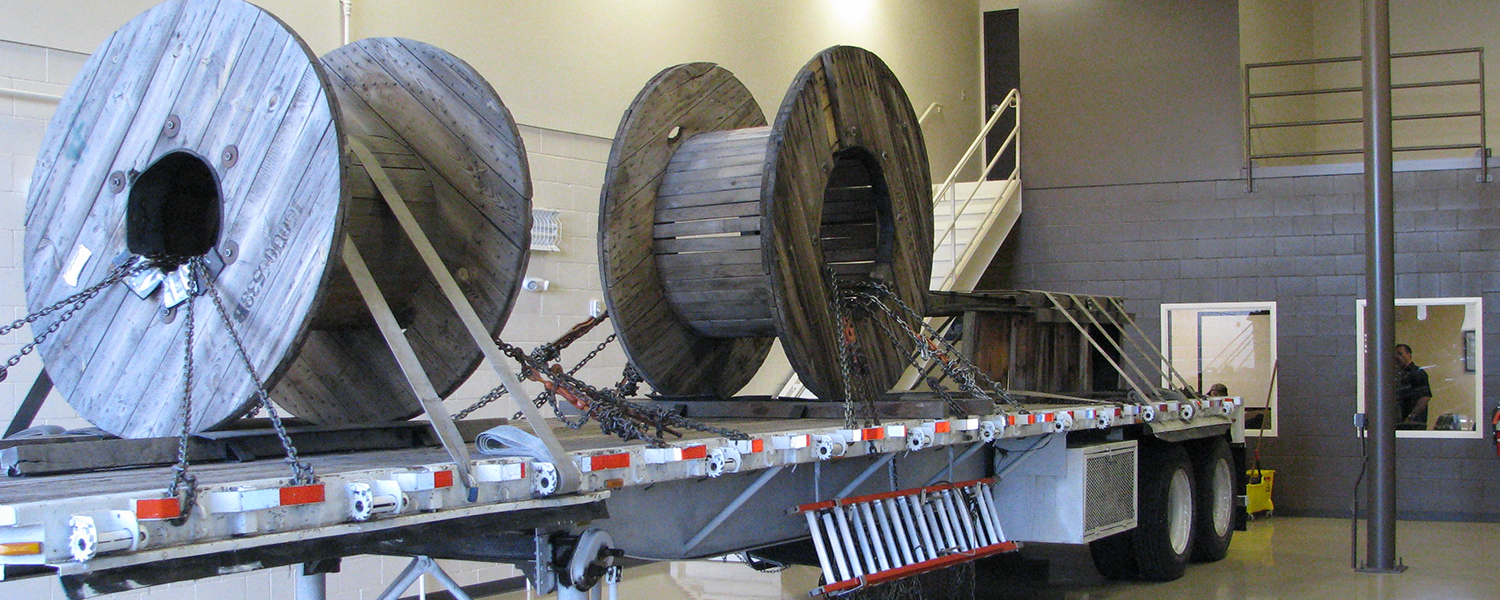
Central Oregon Truck Company: at the forefront of driver safety
For Brad Aimone, director of safety for Central Oregon Truck Company, the numbers are very telling.
“Looking back at 2021, our unsafe driving basic score was 2.5%,” he said. “In 2020, our number was 11.1%, so we saw very measured improvement. Our phenomenal number today is a credit to our drivers, staff and the safety tools we now have in place. It showcases where we sit when it comes to safety.”
Part of the Daseke group of flatbed carriers, Central Oregon Truck Company (COTC) operates 400 trucks and is based in Redmond, Oregon. It’s always been known as a ‘drivers’ company -- it was co-founded by Rick Williams, a former truck driver himself, who now serves as Daseke’s chief operating officer. The company was recently named to the Best Fleets to Drive For Hall of Fame, which recognizes fleets that have made the Top 20 for 10 consecutive years, or 7 consecutive years plus a Best Overall award.
For Aimone, safety is all encompassing and it begins with an extensive new driver orientation program and continues through to ongoing safety education and online training through CarriersEdge. The company also monitors driver performance through SmartDrive inward and outward facing cameras, along with notifications from the truck’s ECU.
Since the company is self-insured through Daseke, safety saves in more ways than one. “Everyone is onboard to its importance for our drivers, and to the bottom line,” said Aimone. “We have a 52-page booklet that documents all the safety practices we have in place and that’s a staple for all the Daseke companies. We strive to develop best practices for all our companies. To ensure compliance, we’ve just starting external audits of our operating companies through a law firm to ensure we are following procedures and Daseke minimum safety standards. Nuclear verdicts are a real thing. We need to make sure we do all we can to protect our drivers, and our companies.”
It begins with orientation
Being a flatbed carrier, the demands for a driver are more hands-on than driving traditional freight. New hires that come onboard (with one year minimal driving experience) go through four days of orientation. “What is a bit different about our orientation process is that the leader of orientation will also be the driver’s coach moving forward,” said Aimone. “This establishes a relationship from the beginning. Over the four days we get the drivers up to speed on our systems, and use of the Eleos platform we use in our cabs; go over load securement with hands-on practice; conduct road tests, which includes tire chaining exercises; and have instruction on ‘safety in motion’ - since working in flatbed is physical, we spend time on proper lifting and movement to avoid soft tissue injuries.”
When COTC does ‘real world’ loading instruction, half the class will be strapping and tying down, while the other half will be on computers doing CarriersEdge modules on Hours of Service and Logbooks, Accident Scene Reporting, Distracted Driving, Practical Cargo Securement Basic Principles (Flatbed), and Vehicle Inspections.
The CarriersEdge Practical Cargo Securement module is unique in the industry as it was developed as a companion piece with the book of the same name published by Techni-Com. “That book is considered the ‘gold’ standard when it comes to securing freight on flatbeds,” said Aimone. “We’ve used it for years, and have the book at each work station. It’s great that the CarriersEdge module works directly with the book so the module reinforces and tests what we study in the book.”
The company’s hands-on training is very thorough. “We have two trailers in our training bay, with students required to use fall protection at all times,” explained Aimone. “One mockup is used for tarp training and securing ductile pipe. The other is set with flat steel, and then coiled rebar. We also have multiple steel coil mockups that can be arranged vertically, in-line, and laterally. All students are given the weight of the product to be secured, and are required to demonstrate the ability to correctly secure all the mockups. What’s more they’re required to demonstrate the construction of bulkheads using dunnage, or grade 70 chains, for flat steel. And they’re required to fully tarp a load within 60 minutes.”
Post orientation drivers must also complete Defense Driving, Practical Cargo Securement (Metal Coils), Trip Planning, and Parking and Deliveries modules within 60 days.
After all practical training is completed, ‘graduation’ from orientation is next. “On the fourth day, the drivers meet our executive team for breakfast,” said Aimone. “From top down it shows our sincere interest in welcoming our new drivers, and their importance to what we do. It also is an open forum with a Q/A. Nothing is off limits. After that, it’s final steps with HR before the driver is ready to hit the road.”
On the road
Each month, Aimone assigns drivers a CarriersEdge module to address any trends the company is seeing when it comes to safety, “or it could be a seasonal training module - driving in winter conditions as example,” he said. “The modules are very well received by drivers - in fact, we had several drivers come to us and ask if we could look at using CarriersEdge in place of the online training platform we were running previously. After pilot testing, and getting great feedback from drivers, we made the switch. Our drivers feel the modules are professional-level training that is pertinent in what they do. And, they are. That’s why we’ve recommended CarriersEdge to all our other operating companies - several have already adopted CarriersEdge.”
According to Aimone, the way the tests are produced helps the drivers retain the information and they can do the work in their cabs at the time that best fits them. “Drivers must score at least 80% to pass the module, and we can see any areas where a driver might be having trouble,” he said. “When we do, the driver’s coach can work directly with the driver for any extra training.
“One thing I appreciate about CarriersEdge is that when they develop new modules they work with some of their customers and do a peer review. They want to make sure their modules are on target and hit the mark. They just don’t roll them out - for example, they had us review their new Weights and Dimensions module. They make sure they’re going to benefit the drivers. And, if it does, it benefits us as well.”
Each quarter Aimone puts together a safety podcast for drivers, which is a “wrap-up” on safety related issues. “We talk about our CSA scores and look at any claims or incidents that might have happened during the quarter, and address things we can all work on. Podcasts are a great tool in communicating with our drivers.”
On the micro side, Aimone said the company will assign specific courses to drivers when they notice either a trend, or specific incident that was flagged by the truck's ECU. “We had a case recently where a driver had a close call when a car was passing the truck, and the sudden swerve from our driver set off an alert,” said Aimone. “The cameras we have documented the incident. Again, a teachable moment for us with the driver, and depending upon the circumstance, we’ll assign a refresher course to help instill proper driving techniques.”
All documented
Keeping drivers abreast of how they’re doing is important,” said Aimone. “We have rolling driver scorecards - giving drivers feedback every four weeks, and then a year-end recap. Safety information is a big part of that. We show the drivers where they stand in claims, the cost of those claims and give them their camera scores and the number of events.”
There’s a saying, “if it’s not documented, it didn’t happen.”
“The scorecards play a part in that for driver improvement. But, documentation is also important to protect our company,” stressed Aimone. “It can come up in a courtroom if you’re being tried for an accident. We can show proof of training delivery, and CarriersEdge makes that easy with their platform.
“We do our absolute best to make sure our drivers are as safe and productive as possible. It’s why we take all the steps we do and work so closely with our drivers. Again, it all comes back to two key words: protect life. It’s something we don’t take lightly.”
Safety is never ending
For Aimone, being a safe fleet means never being complacent. “There is new safety technology constantly being developed and we’re always open to new ideas. You can’t stand pat,” he said. “To survive and flourish in this industry, you have to be proactive and always have your drivers’ back. We do that in many ways, with safety being the most important.”